"Monitor what you make, record what you made"
|
Fast - Accurate Batching
- Prompts operator through schedule of formulas to be batched
- Enforces ingredient tolerances
- Monitors operator productivity
- Optional clean-out batches minimize cross-contamination
Historical Batch Traceability
- What ingredients and lots went into a batch?
- Who batched it?
- When was it batched?
- What were the target and actual amounts?
Track Ingredient Usage
- Receives ingredients into inventory
- Depletes inventory as ingredients used
- Tracks vendor lot numbers from start to finish
- View batches for specified lots, formulas, operators, and dates
Designed for the Environment
- Ruggedized equipment on the plant floor
- PC stays in the office
- Off-the-shelf standard components
- Modular, easy to maintain design
|
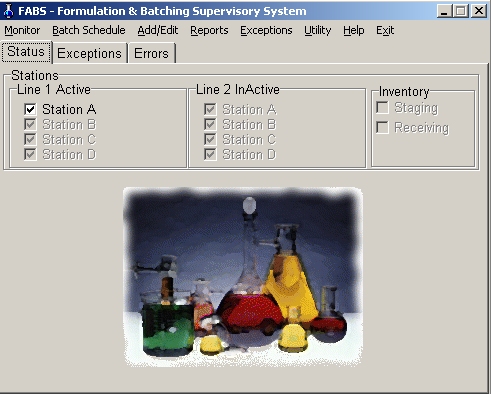
Working in conjunction with the
superb Weigh-Tronix WI-130/WPI-135/1310 Weight Display, The FABS Formulation and
Batching Supervisory System controls and monitors the manual fill of ingredients
into a scale mounted container.
The FABS System consists of two
software components. The first program resides in the WI-130/WPI-135/1310 Display on the
factory floor and controls the manual filling of multiple ingredients, by
weight, into a container on the scale. The second program resides in a remote PC
and monitors the filling operation and collects data from the filling process.
The PC program then provides complete record keeping and reporting for
management control of the filling process.
The FABS System can accommodate up
to two separate filling lines with up to four active filling stations/scales per
line. Transactions for all active stations and lines are constantly monitored
and recorded at the remote, PC location. The PC operator can watch the results
of each filling operation and can modify and download new formulas to each
station separately, as the process requires.
|
|
At the filling station, the scale
weight display prompts the operator through each stage of the filling process,
displaying each formula and the associated ingredients for the formula.
The WI-130/WPI-135/1310 monitors the filling of each ingredient and prevents the operator from
under filling or overfilling the ingredient target weight.
|
|
The WI-130/WPI-135/1310 then records the results of each batch and transmits the completed batch information
back to the remote PC system.
|
|
The unique display of the weight indicator provides the
scale operator with detailed and exact information to make the filling process
accurate and efficient.
|
|
|
Top of Page
Seed Blending System
Six (6) individual hoppers, equipped with a variable speed vibratory feeder,
are mounted on load cells. The operator
enters a blend/formula number into the weight indicator/controller, which
controls output proportionately. Each feeder dispenses onto a
takeaway conveyor which eventually feeds into a "finished mix" hopper
with bagger.
Operation
Controller Setup:
1) Supervisor enters the various blend numbers and their
percentage per hopper requirements
2) There could be formulas where all 6 hoppers are not used,
as in the case of simple blends that are only a three or four variety mix
Operator Sequence:
1) Once all the supply hoppers have been filled, a blend number is
entered into the 1310 using the keypad
2) Upon verification of correct blend number the 1310 prompts to "PRESS START BUTTON"
3) Operator depresses start button, 1310 energizes the appropriate feeders
with an output level signal and begins to monitor weight loss/time long enough
to establish the appropriate output level to send for each hopper so as to get
the correct blend
4) There is an automatic/manual switch on the control panel for times
when there is a need to empty individual supply hopper and/or other requirements
FABS Software and Hardware Specifications
Software Specifications
|
|
Scale Support
|
|
|
|
Scale Operating
System
|
|
Network Support
|
|
Compatibility and
Data Storage
|
|
Security
|
|
Barcode
Specification
|
|
Production Scheduling
|
|
Inventory
|
|
Reports
|
|
Online Help
|
|
Remote Support
|
|
|
Hardware Specifications
|
Pentium
II processor or greater
-1 GB available hard disk space
-256 MB RAM
-PC Anywhere 10.0 with modem or Internet connection
-Uninterruptible Power Source (UPS)
-Network Connectivity
-RS232
serial port (for Serial version)
|
Computer Location
|
|
Scale
|
|
Communication
|
|
Network
|
|
Scanner
|
|
Printer
|
|
Support
|
|
|
Top of Page
|
|
include("../footer2.htm"); ?>
|